
Manufacturers must seek out solutions that link people, technologies, and data to expedite innovation and bring ideas to fruition faster than ever before. (Pic source – Shutterstock)
Navigating trends and challenges through technology in the manufacturing industry
Article by Hexagon MI Malaysia.
The manufacturing industry is a key pillar of economic growth and innovation, playing a vital role in driving progress across various sectors. Over the years, it has witnessed a multitude of transformations driven by technological advancements, propelling it forward into new frontiers.
As we stand at the precipice of the Fourth Industrial Revolution, technology continues to redefine the manufacturing industry, offering unprecedented opportunities and challenges. The impact of technology on the manufacturing sector is now more profound than ever before. Navigating these trends and challenges by harnessing the power of technology is crucial for businesses to thrive in a rapidly evolving global market.
Additionally, integrating both technology and human skills can lead to synergistic outcomes in the manufacturing industry. This approach allows businesses to leverage the speed and precision of technology while also utilizing the critical thinking and problem-solving abilities of skilled workers.
“As a company that works closely with customers in manufacturing—and as a manufacturer ourselves, we have a deep understanding of these industry dynamics,” said Khoo Siew Fang, the Country Manager of Hexagon MI Malaysia.
Examining these trends and challenges from a macro perspective reveals four primary categories: enhancing productivity through digitalization, managing costs for increased profitability, promoting sustainability, and dismantling silos.
Increasing productivity for the manufacturing industry
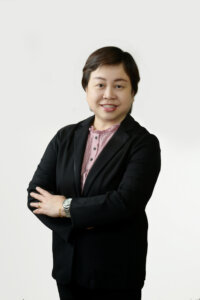
Khoo Siew Fang, the Country Manager of Hexagon MI Malaysia.
Embracing digitalization is paramount for enhancing productivity in the manufacturing industry. The adoption of advanced technologies such as artificial intelligence, robotics, and the Internet of Things (IoT) enables streamlined processes, optimized operations, and improved efficiency. Automation, for instance, reduces human error, increases output, and enables round-the-clock production.
Oftentimes, businesses face challenges in fully utilizing data. Now that smart factories are becoming a reality, real-time data analysis and predictive analytics empower manufacturers to make data-driven decisions, identify bottlenecks, and optimize their supply chains. By digitizing and storing data, businesses can make decisions faster and collaborate more effectively. Digital tools like project management software, communication platforms, and data analytics optimize workflows and identify areas for improvement. Overall, embracing digitalization can lead to increased efficiency and productivity in various sectors.
By embracing digitalization initiatives that strengthen the connectivity of digital data, manufacturers can significantly boost productivity. In fact, McKinsey reports that digital transformation may lead to a 15-30% increase in labor productivity and a 30-50% reduction in downtime for manufacturers.
Managing costs to drive profitability
Managing costs is essential for increased profitability, optimizing financial performance, and maximizing the bottom line. This involves analyzing expenses, negotiating better deals, implementing cost-saving measures, and streamlining operations for long-term success. In late 2021, the BCIS Materials Cost Index reported that global material costs had reached a 40-year high, underscoring the growing importance for manufacturers to effectively manage costs to remain successful.
To combat the escalating costs of raw materials and labor, manufacturers need to ensure their end-to-end processes are interconnected and optimized. By implementing closed-loop workflows across departments and promoting agility, seamless data exchange can be achieved—enabling manufacturing companies to streamline operations and boost profitability in the face of rising expenses.
Further, the implementation of advanced analytics and predictive maintenance can help identify maintenance needs and prevent costly downtime. Furthermore, optimizing inventory management through data-driven insights minimizes waste and excess stock, leading to substantial cost reductions. By leveraging technology to streamline processes and optimize resource allocation, manufacturers can improve their bottom line and gain a competitive edge.
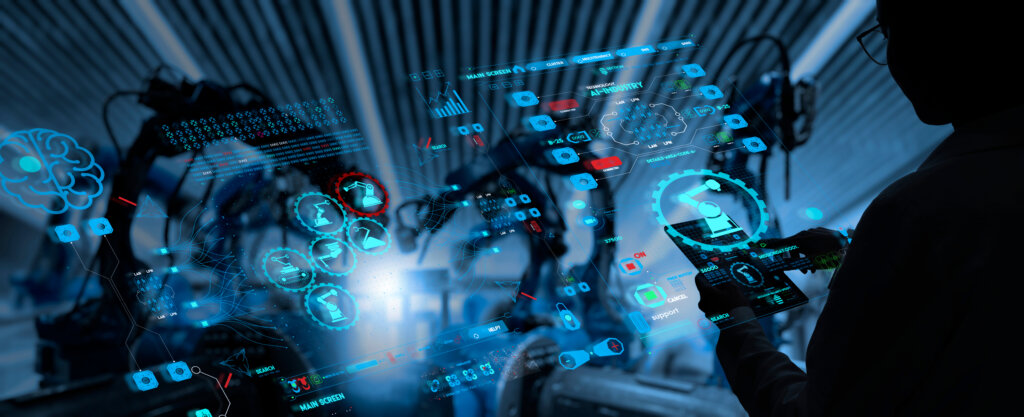
Sustainable manufacturing is on the agenda for businesses. (Pic source – Shutterstock)
Fostering sustainability
The urgent need to address environmental concerns and comply with regulatory requirements has made sustainability an imperative for the manufacturing sector. Beyond environmental impacts, businesses must consider economic sustainability, resource production and consumption, social responsibility, and other factors to remain competitive in an evolving market. Connected systems empower manufacturers to think about sustainability holistically, providing tools and insights to make informed decisions and reduce negative impacts.
For example, the adoption of green manufacturing practices, such as energy-efficient processes and eco-friendly materials, reduces the industry’s carbon footprint. Additionally, the implementation of circular economy principles, including recycling and waste reduction, contributes to a more sustainable manufacturing ecosystem. Through technology-enabled sustainability initiatives, manufacturers can align their operations with environmental goals, bolster their brand reputation, and meet the demands of eco-conscious consumers.
Breaking down silos in the manufacturing industry
Manufacturing ecosystems consist of diverse facilities, such as OEMs and suppliers, with teams collaborating remotely on product development. Both internal and external silos can hinder progress, making digitalization essential for breaking down these barriers. McKinsey estimates that digital collaboration could unlock over $100 billion in value for the industry — meaning manufacturers must adopt digitally connected solutions to promote collaboration and interaction across departments.
In response to evolving industry trends and challenges, manufacturers must seek out solutions that link people, technologies, and data to expedite innovation and bring ideas to fruition faster than ever before. By navigating these trends through technology, manufacturers can stay ahead of the curve and unlock new possibilities.
The views in this article are those of the author and may not reflect the views of this publication.
READ MORE
- 3 Steps to Successfully Automate Copilot for Microsoft 365 Implementation
- Trustworthy AI – the Promise of Enterprise-Friendly Generative Machine Learning with Dell and NVIDIA
- Strategies for Democratizing GenAI
- The criticality of endpoint management in cybersecurity and operations
- Ethical AI: The renewed importance of safeguarding data and customer privacy in Generative AI applications